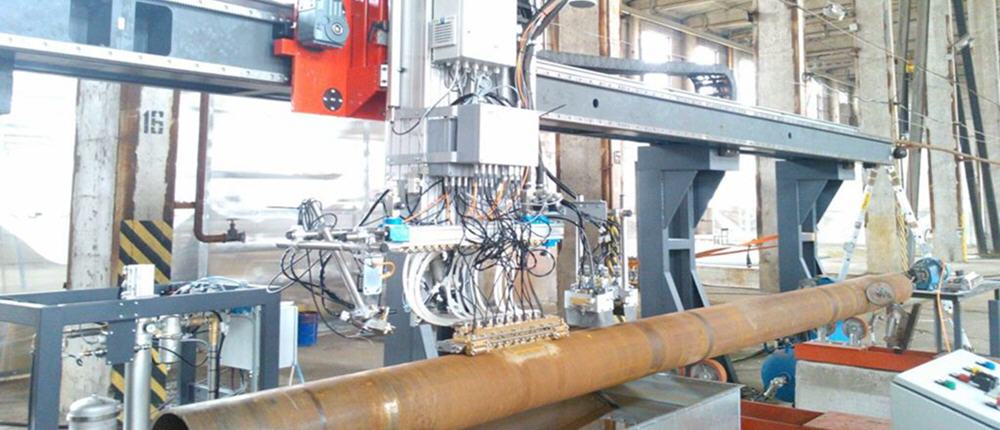
Ультразвуковой контроль электросварных и бесшовных труб малого и среднего диаметра
ULTRATUBE - установка ультразвукового контроля электросварных и бесшовных труб малого и среднего диаметра
Система ультразвукового неразрушающего контроля ULTRATUBE позволяет выполнять:
- обнаружение дефектов и толщинометрию тела трубы;
- выявление продольных и поперечных дефектов сварного шва и околошовной зоны сварного соединения (зоны термического влияния);
- обнаружение расслоений на концах труб.
Ультразвуковой контроль электросварных и бесшовных труб проводится с целью выявления и отбраковки изделий, имеющих недопустимые дефекты продольной и поперечной ориентации, расслоения основного металла, отклонения от предельно допустимых размеров по толщине стенки.Установка обеспечивает автоматизированный УЗК электросварных и бесшовных труб при помощи подсистем контроля продольных и поперечных дефектов, подсистемы толщинометрии.
Ультразвуковой контроль осуществляется эхо-методом. В установке реализован совмещенный режим работы акустических преобразователей. Необходимые параметры и допуски при контроле обеспечиваются настройкой аппаратуры на стандартных образцах.
Особенности оборудования
Автоматизированная установка неразрушающего контроля качества электросварных и бесшовных труб ULTRATUBE является сложным техническим комплексом включающим:
- механическое оборудование;
- пневматическое оборудование;
- электронно-акустическую систему контроля;
- систему автоматического управления;
- управляющий вычислительный комплекс;
- систему электропитания.
Механическое оборудование осуществляет функцию обеспечения акустического контакта ПЭП или ЭМАП с трубой при движении с заданной скоростью через измерительные модули УЗК.
Электронно-акустическая система контроля обеспечивает сплошное непрерывное сканирование металла движущейся трубы с помощью двух измерительных модулей. Измерительные модули подсистем контроля поперечных дефектов, продольных дефектов и толщинометрии в установке конструктивно разделены.
Формирование зондирующих импульсов, прием и первичная обработка эхо-сигналов обеспечивается аппаратурой ультразвуковой электроники. Полученные данные ультразвукового контроля в цифровом виде передаются в вычислительный комплекс для дальнейшей программной обработки.
В установках ULTRATUBE применяются методы непрерывной ультразвуковой диагностики электросварных и бесшовных труб малого и среднего диаметра из низкоуглеродистых и низколегированных сталей. Работа системы базируется на применении методов ультразвуковой дефектоскопии, включающих прохождение, отражение и трансформацию ультразвуковых колебаний в металлах.
Непрерывное сканирование трубы осуществляется с помощью пьезоэлектрических (ПЭП, ПФР) или электромагнитно-акустических преобразователей (ЭМАП), причем ультразвуковой контроль может выполняться как с помощью обычных пьезоэлектрических преобразователей, так и с применением фазированных решеток (Phase Array).
Фазированная решетка обеспечивает сканирование в режиме реального времени сечения сварного шва под различными углами. Это позволяет регистрировать неблагоприятно ориентированные опасные дефекты в сварном шве.
В установке реализованы дополнительные схемы прозвучивания, регламентируемые специальными требованиями - контроль поперечных дефектов в околошовной зоне, On-Bead, TOFD.
Конструкция и размещение акустических преобразователей обеспечивают расположение акустического фокуса в области противоположной стенки материала труб с целью получения максимальной амплитуды эхо-сигнала.
В каждом такте контроля один из акустических преобразователей формирует объемную продольную волну, распространяющуюся по нормали к поверхности трубы.
Цикл контроля одного участка трубы может состоять из нескольких тактов с осуществлением накопления принимаемых сигналов, что позволяет уменьшить уровень шумов и помех, снижающих качество неразрушающего ультразвукового контроля.
Кабельные соединения, по которым передается зондирующий импульс, являются элементами согласования акустического тракта. Большое значение при этом имеют параметры передающей линии, которые определяются, в основном, ее длиной и маркой кабеля.
Все блоки контроля размещаются на подвижном модуле (платформе), обеспечивающем их перемещение вдоль вращающейся трубы при её сканировании.
На каждую дефектную трубу распечатывается протокол контроля со схемой расположения дефектов (дефектограммой). Дефектные сечения трубы отмечаются краской.
Варианты исполнения оборудования
- Портального типа – труба во время контроля вращается на поворотных роликах, а измерительный модуль движется вдоль трубы, сканируя весь её периметр. При этом возможна как продольная (поступательная), так и поперечная загрузка выгрузка трубы в зону контроля.
- Стационарного типа – труба движется вращательно-поступательно через зону контроля. При этом неподвижный измерительный модуль сканирует всю трубу во время ее транспортировки через зону контроля.
Управляющий вычислительный комплекс
Управляющий вычислительный комплекс организует:
- контроль качества в соответствии с установленными правилами отбраковки;
- оперативную диагностику;
- сортировку труб;
- отображение информации о дефектных зонах, сопровождение их изображения на мнемосхеме;
- классификацию несплошностей на "допустимые" и "недопустимые";
- сигнализацию недопустимых дефектов и выдачу управляющего сигнала на включение дефектоотметчика;
- печать протоколов контроля, архивирование и хранение;
- связь с ЭВМ высшего уровня (интегрированная система).
Система контроля качества сварных соединений и зоны термического влияния
Слежение за положением сварного шва трубы осуществляется с помощью бесконтактного лазерного сканера и, при необходимости, выполняется автоматическая корректировка положения трубы на роликах.
Система контроля качества шва и околошовной зоны (зоны термического влияния) состоит из нескольких преобразователей.
Используемая в контроле сварного шва и околошовной зоны TOFD-схема обеспечивает выявление дефектов произвольной ориентации в средней части сварного шва, в том числе дефектов имеющих малое раскрытие. Данная схема может дополнять (или замещать) схему TANDEM. Кроме того, TOFD обеспечивает определение реальных размеров дефектов.
Система контроля толщины и расслоений металла
Каналы подсистемы толщинометрии работают в совмещенном режиме контроля. Подсистема зондирования включает: акустический преобразователь, генераторно-усилительные блоки, блок развязки.
Для контроля толщины и выявления расслоений стенки прозвучивание осуществляется по радиусу.
Система контроля внутренних дефектов
Система обеспечивает обнаружение продольных и поперечных дефектов в металле трубы. Прозвучивание трубы в процессе контроля осуществляется по окружности - для выявления продольных дефектов, а также вдоль образующей, по ходу движения трубы - для выявления поперечных дефектов.
Дефектоскопическая электроника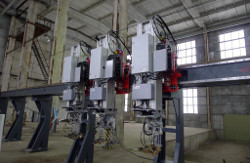
Дефектоскопическая электроника смонтирована в компактных блоках имеющих класс защиты IP67 (в соответствии с международным стандартом IEC 60529, а также DIN 40050, ГОСТ 4254-96), а также обеспечивающих полную электромагнитную совместимость с оборудованием Заказчика.
Каждый блок дефектоскопической электроники может содержать до 32 прямых (без коммутации) каналов.
Новая дефектоскопическая электроника потребляет в 8 раз меньше электроэнергии по сравнению с аналогичным оборудованием других фирм-производителей, а значит, имеет меньшее тепловыделение, что позволяет не использовать дорогостоящее и ненадежное в условиях завода жидкостное охлаждение радиоэлектронной аппаратуры.
Калибровка оборудования
Оборудование позволяет в автоматическом режиме проводить регулярную калибровку по стандартному образцу (СОП).
Настройка чувствительности и проверка работоспособности системы производится по контрольным отражателям в виде сверлений заданным диаметром или пазов по условиям стандартов (ГОСТ, API 5L, DNV и др).
Доступно два вида калибровки:
- по малоразмерному СОП с искусственными дефектами с автоматической загрузкой / выгрузкой СОП;
- по полноразмерной трубе с искусственными дефектами в технологической линии.
Оценка качества
Оценка качества производится в соответствии с требованиями стандартов API 5L, ГОСТ 31447, ГОСТ 14782; ISO 3183, DNV-OS-F101, Shell Technical Specifications, Specification INTECSEA, специальные требования TRANSNEFT, GAZPROM (в том числе по спецификациям проектов Shtokman, Nord Stream).
Характеристики объектов контроля (труб малого и среднего диаметра)
Характеристика | Значение |
Типы контролируемых труб | Трубы малого и среднего диаметра, бесшовные и сваренные сваркой типа ERW и LBW |
Качество поверхности трубы | После прокатки |
Диаметр труб | 50 – 630 мм |
Длина труб | до 18,5 м |
Толщина стенки трубы | до 50 мм (больше 50 мм – опционально) |
Производительность | до 150 труб/час |
Видеоматериалы работы оборудования